Mesh Topology Illustration for Fuel Injector
- Yanhao Zhu
- 2016年5月22日
- 讀畢需時 2 分鐘
Gasoline Direct Injection (GDI), has been regarded as the most popular strategy for fuel economy improvement of SI engines for year. However, there is a unexpected fuel injection during the bounce caused by the impact between needle and hardtop.
In order to minimize the fuel leakage, I was given to chance to help Ford and its research team on the CFD simulation of fuel injector. One of the biggest challenge we've faced lies in mesh generation: Not only do we want a high-quality mesh, we also want it to endure some node displacement without losing too much orthogonality. We eventually find its way out with 3 weeks' effort. This blog might be helpful to CAE engineers in related field; it can also be a nice illustration on how structured mesh should be built on the topological pattern.
The following figure shows the boundary condition:

We need to map the physical domain to the topology space before mesh generation. The blocking and mapping of domain requires a sense of spacial imagination. It should be noticed that only rectangle area or part of a rectangle is allow in 2D case, simplifying the procedures in our case. The geometry in physical space looks like a bended letter 'L' so we followed the idea listed below:
1) A rectangular block is created and divided into four small pieces;
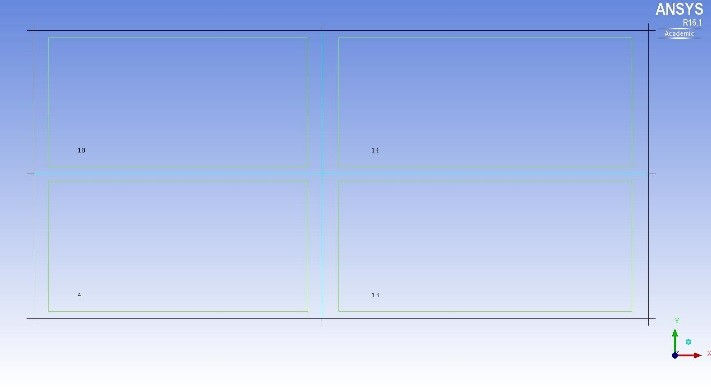
2) The right bottom piece is deleted;

3) The right top rectangle is further divided into several pieces for mapping;

4) Map the edge with the corresponding line in physical space.

After setting the number of nodes on each edge, we can generate the structured mesh for physical domain:

Generating a structured mesh is generally more time-consuming than building a unstructured one, but you can tell from the mesh quality check that it worth the effort!

By replacing an unstructured mesh with a structured one, we can easily tolerate a 50-micron displacement, more than twice as much as what we want. We further compared the injection rate between the dynamic case and the static case and finally got the result that Ford expected from us.

Comments